船舶建造焊接机器人流行到什么程度?
目前我国船舶建造主要依靠手工焊接为主,焊接技术水平大多数处于半自动化到自动化焊接阶段,相比较发达国家而言焊接自动化程度较低。
船舶的建造离不开焊接,随着技术的发展,从最开始的手工焊接、机器人示教焊接,到现在的可自动识别焊缝再进行焊接的柔性系统,手工焊接逐渐成为过去,机器人焊接成为主流。机器人焊接较传统焊接方法优势明显,普通六轴机器人的焊接速度(50~160cm/min)高于手工焊接(40~60cm/min),且机器人在焊接过程中焊接参数恒定性好、质量稳定性高、美观性强、焊渣少,减少了后续清渣打磨工序,使得焊接自动化成必然趋势。
船舶管道焊接机器人技术
船舶建造过程主要分为船体和管道的加工,管道生产加工占船舶建造总工时的8%~12%,常见的管道结构类型有直管、弯管、锥形过渡管、偏心过渡管、等径三通管及马鞍形连接管等。由于其多样化、多品种、离散性的特点,使得手工焊在管道加工过程中容易出现成形质量差,合格率较低等情况,因此对管道焊接自动化的研究从未停止。首先是管道焊接过程中的对接问题,传统的管道对接焊主要依靠工人经验,先在管道连接处进行划线、定位、定位焊后再进行焊接,这不仅不能保证高效率和高质量,而且很费时。
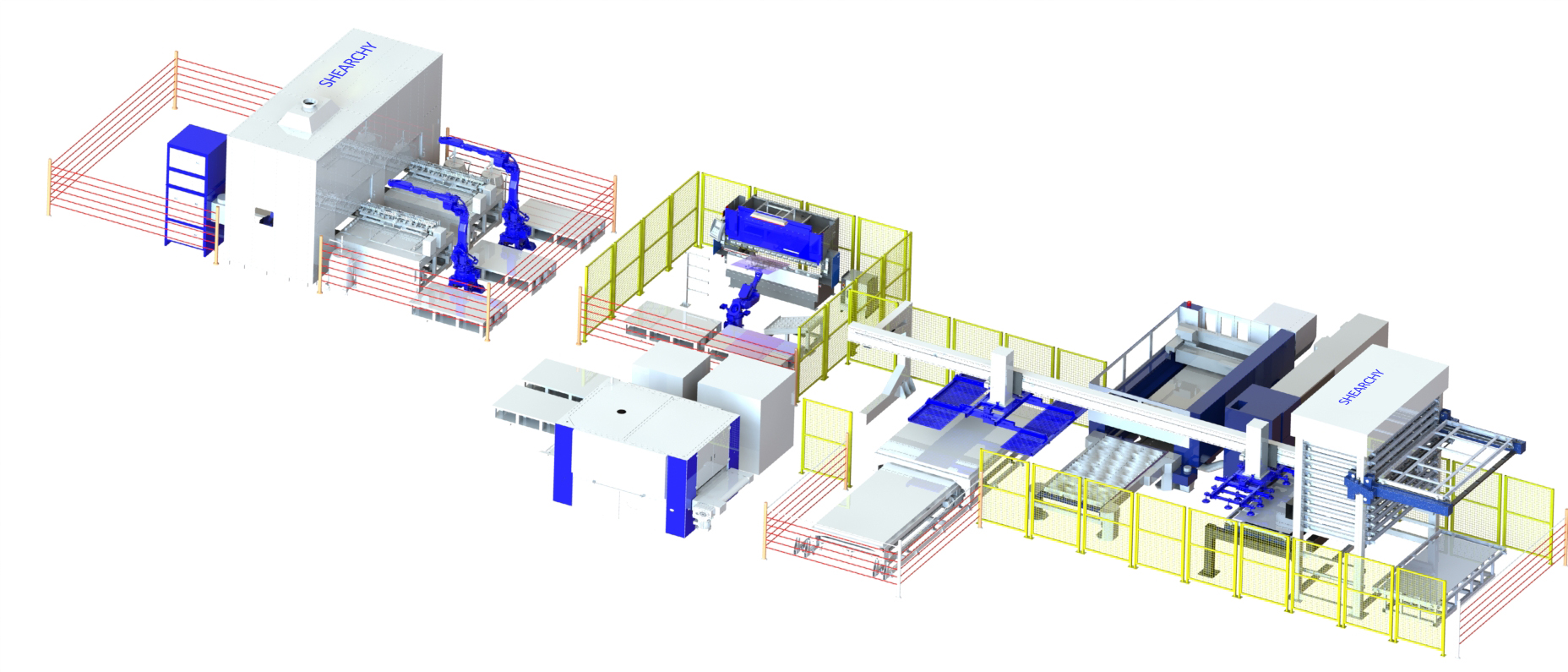
针对船舶管道对接问题,开发了一种新型船舶管道焊接辅助装置,该结构结合液压电子锁装置,能够更方便、更可靠地对齐、居中和锁定两条焊接管道;其次是管道焊接机器人装备的设计,结合机器人位置传感技术、电弧跟踪技术、机器人协同主从控制技术,以及开启式变位机链轮传动装置和MIG自动焊接专家系统等,研发了国内第一条船用管-管、管-法兰主从机器人焊接生产线。
为了提高复杂环境下的管道焊接工艺研究了管道焊接工艺方法,该焊接方法与传统钨极氩弧焊相比,允许在靠近钨极区域切向导入焊丝,并被整合到喷嘴中,使得焊枪更加紧凑,便于机器人的操作,在管道打底焊过程中焊丝的焊接速度和熔化速度提高两倍。在焊接过程中除了控制焊接速度、电弧电压、焊接电流等因素外,电弧的弧长也是一个重要的因素,它直接影响焊接过程中飞溅的产生、焊后焊缝成形等。
对于电弧的控制也是众多学者研究的方向,针对管-板焊接过程中弧长的不稳定性,搭建了直流脉冲氩弧焊机、激光传感器和CCD相机试验平台,利用激光传感器测量钨极和管-板之间的距离,采用CCD相机结合分度尺获得管-板水平和垂直方向的校准图像标定、图像预处理、图像特征值提取等,可以实时控制焊枪与管板间间距,有利于焊缝成形。